Deposit geology
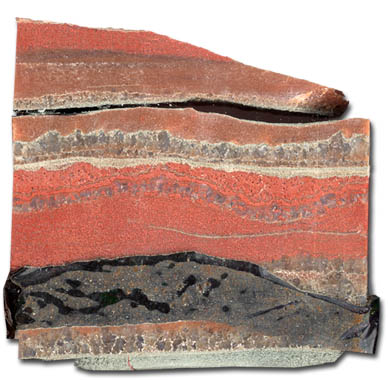
Ore mining technology
At present time the seams which are being mined are the seams of the 2nd and 3rd potash levels (seams II and III). The potash seam of the 1st level at PU 1 is being mined since 2004. The potash seam of the 4th level is considered as reserves projected be mined in the future.Mining methods:
1. Chamber mining
The development of the deposit was started by the chamber system the mining. This mining technique prevents dangerous deformations of the underworked rock mass and consequently eliminates the penetration of underground water into the mined-out area. The following types of chamber mining are used within the deposit:
- Mining with yielding pillars establishing
- Mining with support pillars establishing
- Mining with regular yielding and support pillars establishing
2. Pillar mining
JSC Belaruskali is the only one mining company which uses pillar mining technique for the development of salt deposits.
The pillar mining of the 2nd and 3rd potash seams by longwall mining (face mining) with roof collapse is used since 1969.
The following types of pillar mining are used:
- Complete mining of the 2nd seam and the layers II, II-III and III of the 3rd seam without longwall slicing
- Selective mining of the layers II, II-III and III of the 3rd seam without longwall slicing
- Layer mining of the 2nd seam
- Layer mining of the 3rd seam
At present time about 70% of ore is mined using longwall mining technique (faces 180-300 m long).
3. Combined system of mining
The 3rd potash level has three productive sylvinite layers (II, III and IV) divided by seams of halite. When using the combined system of mining, the upper (IV) sylvinite layer is mined using the pillar technique and the subjacent layers (II and III) are mined by the chamber method of mining. This system is used rather seldom due to a big loss of the mineral from the layers II and III.
4. Development workings
The development workings within the deposit are driven by continuous mining complexes, which consist of a continuous miner, a conveyor hopper and a shuttle car. The workings are 3.0, 4.0, 4.05, 4.5 m wide (depending on the type of continuous miners used and the purpose of the working).
The height is 2.4, 2.6, 3.0 m. The floor of the working can be undercut if necessary.
The company developed and implemented the unique process methods and equipment which know no equals in the world mining practice. The company uses the modern mining equipment manufactured by leading global producers.
When sylvinite and halite are extracted separately the content of potassium chloride in the mined ore raises up to 30-35% because in this case only sylvinite layers are extracted, while halite is left underground.
To maximize the degree of mineral extraction the company carries out the scientific researches and successfully implements the pillarless mining schemes, which aim to increase the operating life of mines.